Discover What is Porosity in Welding and Its Effect on Structural Honesty
The Scientific Research Behind Porosity: A Comprehensive Overview for Welders and Fabricators
Understanding the detailed systems behind porosity in welding is critical for welders and fabricators striving for remarkable craftsmanship. From the structure of the base products to the ins and outs of the welding process itself, a plethora of variables conspire to either exacerbate or minimize the presence of porosity.
Recognizing Porosity in Welding
FIRST SENTENCE:
Assessment of porosity in welding exposes vital insights into the stability and high quality of the weld joint. Porosity, defined by the visibility of dental caries or gaps within the weld steel, is an usual concern in welding processes. These voids, otherwise effectively resolved, can jeopardize the structural integrity and mechanical properties of the weld, causing possible failures in the ended up item.
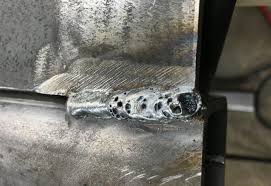
To identify and measure porosity, non-destructive screening techniques such as ultrasonic testing or X-ray inspection are typically employed. These techniques enable the recognition of inner defects without compromising the integrity of the weld. By evaluating the size, form, and distribution of porosity within a weld, welders can make enlightened choices to boost their welding procedures and accomplish sounder weld joints.
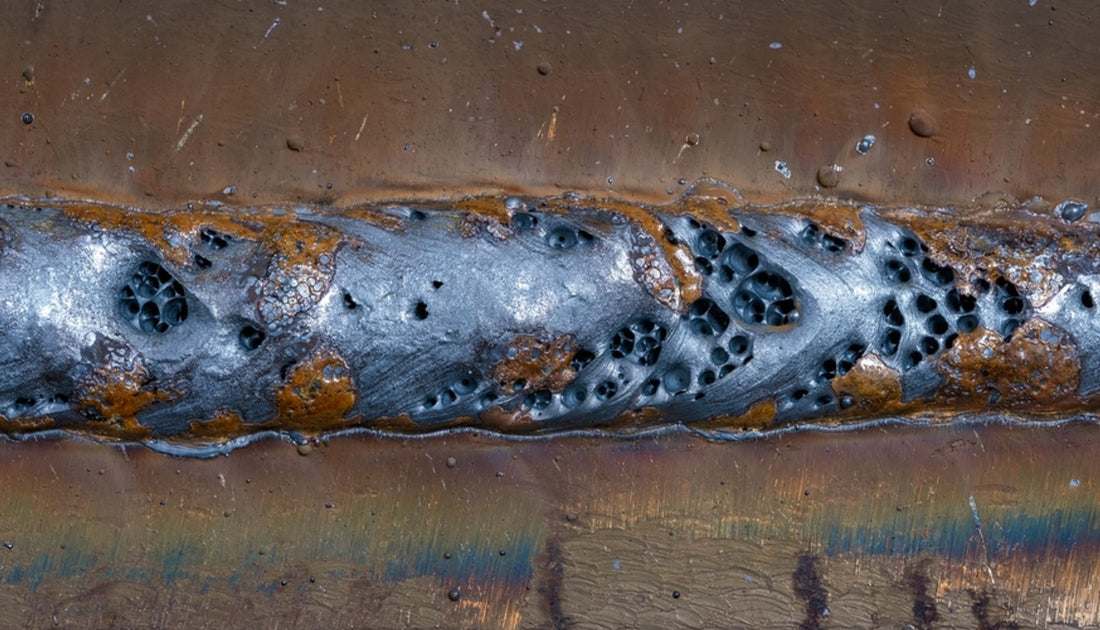
Elements Affecting Porosity Development
The event of porosity in welding is affected by a myriad of variables, varying from gas securing effectiveness to the ins and outs of welding parameter setups. One critical variable adding to porosity formation is inadequate gas shielding. When the shielding gas, normally argon or carbon dioxide, is not successfully covering the weld pool, atmospheric gases like oxygen and nitrogen can pollute the liquified steel, causing porosity. Furthermore, the tidiness of the base products plays a considerable duty. Pollutants such as corrosion, oil, or wetness can vaporize during welding, creating gas pockets within the weld. Welding parameters, including voltage, current, take a trip speed, and electrode kind, also impact porosity development. Using incorrect settings can generate extreme spatter or warm input, which in turn can cause porosity. Moreover, the welding method utilized, such as gas metal arc welding (GMAW) or secured steel arc welding (SMAW), can affect porosity development because of variations in warmth circulation and gas insurance coverage. Understanding and regulating these elements are essential for lessening porosity in welding procedures.
Results of Porosity on Weld Quality
Porosity development considerably endangers the structural stability and mechanical properties of bonded joints. When porosity is present in a weld, it produces gaps or cavities within the material, minimizing the general toughness of the joint. These gaps work as tension concentration factors, making the weld extra susceptible to splitting and failure under load. The presence of try this web-site porosity also deteriorates the weld's resistance to deterioration, as the entraped air or gases within the voids can react with the surrounding environment, resulting in degradation in time. Furthermore, porosity can hinder the weld's ability to endure pressure or impact, more jeopardizing the overall top quality and reliability of the welded structure. In essential applications such as aerospace, auto, or architectural building and constructions, where security and toughness are extremely read review important, the detrimental results of porosity on weld high quality can have serious repercussions, emphasizing the relevance of decreasing porosity via correct welding methods and procedures.
Strategies to Lessen Porosity
Additionally, making use of the appropriate welding specifications, such as the appropriate voltage, present, and take a trip rate, is important in protecting against porosity. Keeping a consistent arc size and angle throughout welding also helps reduce the possibility of porosity.

Moreover, choosing the ideal protecting gas and preserving appropriate gas flow rates are important in reducing porosity. Using the suitable welding technique, such as back-stepping or employing a weaving movement, can likewise assist disperse warmth equally and minimize the possibilities of porosity formation. Guaranteeing proper air flow in the welding setting to eliminate any potential resources of contamination is vital for attaining porosity-free welds. By implementing these strategies, welders can properly reduce porosity and produce top notch welded joints.
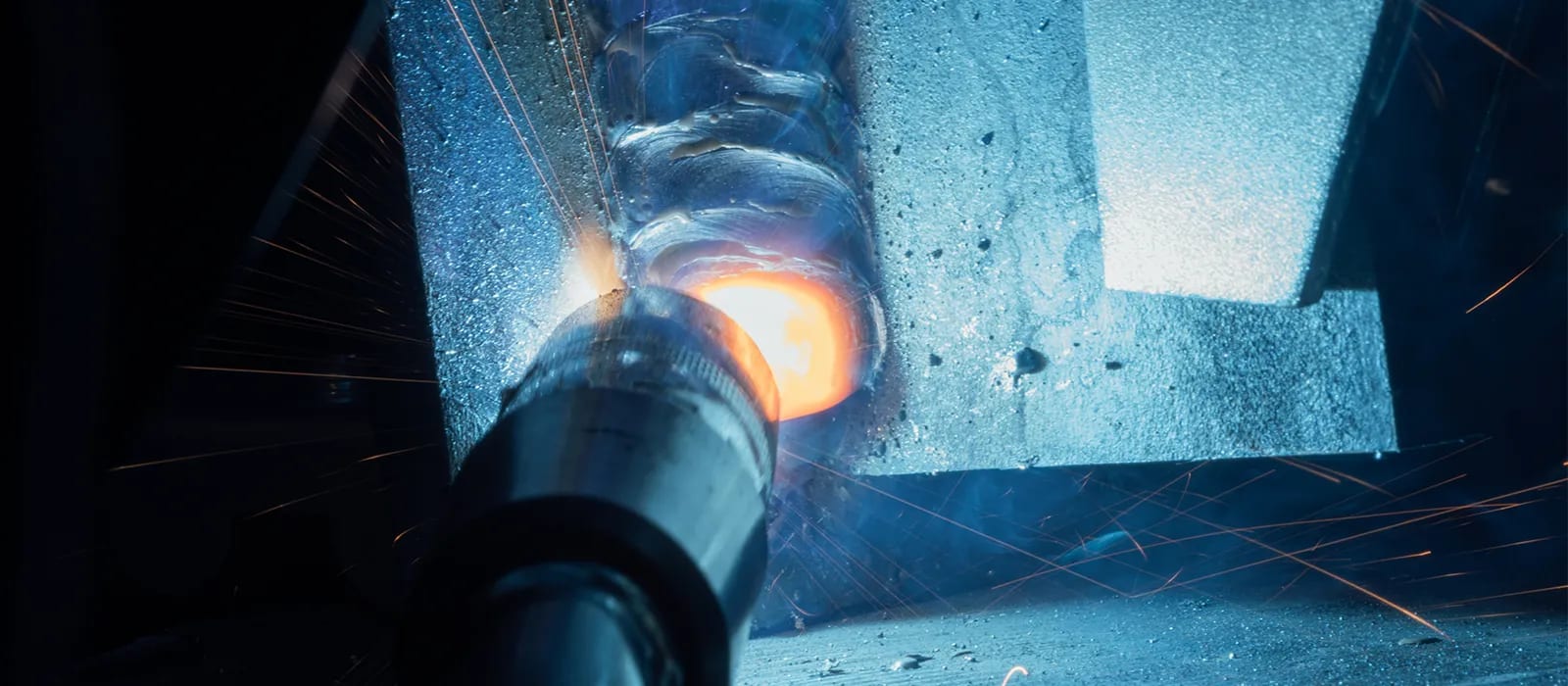
Advanced Solutions for Porosity Control
Executing sophisticated innovations and ingenious methods plays an essential duty in accomplishing premium control over porosity in welding processes. Additionally, utilizing innovative welding strategies such as pulsed MIG welding or modified environment welding can also assist alleviate porosity concerns.
One more innovative solution includes the usage of advanced welding equipment. Making use of tools with integrated attributes like waveform control and innovative power resources can boost weld quality and reduce porosity risks. The application of automated welding systems with exact control over specifications can considerably reduce my explanation porosity problems.
Moreover, integrating sophisticated surveillance and inspection innovations such as real-time X-ray imaging or automated ultrasonic testing can aid in spotting porosity early in the welding process, enabling immediate corrective actions. In general, incorporating these innovative options can considerably enhance porosity control and improve the overall quality of welded components.
Final Thought
To conclude, understanding the science behind porosity in welding is essential for welders and makers to create top quality welds. By determining the elements influencing porosity formation and applying methods to reduce it, welders can boost the overall weld top quality. Advanced solutions for porosity control can further enhance the welding procedure and ensure a strong and reliable weld. It is crucial for welders to continuously enlighten themselves on porosity and execute best techniques to accomplish optimum outcomes.